The Problem
Detroit Renewable Power has a 65 MW GE steam turbine that carries the major load for Detroit’s city’s steam system. It sends out on cool days up to 500,000 lbs of steam per hour. The turbine had not been maintained well and the current owners of the plant had very little documentation on the existing equipment.
To execute the outage we had to not only deal with the turbine and the generator with little to no documentation but also we had to learn, understand and repair the condenser isolation system.
Additionally, the plants turbine controls and excitation controls were antiquated and in desperate need of an upgrade.
Our Results
-
The turbine produced 12% more MW resulting in an additional revenue of $1.6 million annually.
-
The Turbine was able to send out an additional 50,000 pounds of steam per hour to the city of Detroit
-
Hydrogen use went down 85% because we found and corrected the source of the leak in the seals
How We Did It
We wrote the turbine repair spec and solicited bids from GE, Elliot and Turbocare. We performed a bid evaluation and selected Turbocare for the work and Siemens for the Controls and Exciter work. We went through the plants warehouse, identified and pulled all of the spare the plant had for the turbine We performed a gap analysis between what the plant had and what the plant needed in regards to spare parts to execute the turbine outage. We then sourced and ordered all the required spares for the turbine (approx... $250K)
We planned the turbine outage and trained each member of both the Ops and Maintenance Departments on their turbine.
When the casing came apart it was discovered that the turbine had thrown a blade on its 11th stage and lost a shroud on its 4th stage. This was an unplanned discovery and we had to react. We shipped the bearings and Hydrogen seals to Cleveland Ohio. Blades were reverse engineered and being produced in Manchester, CT. Packing was being made in Chicopee MA. We shipped to the rotor to Houston.
Additionally we found the following:
The turbine was found 10 mils low to the generator and should be 10 mils high
Packing rows 24,25,26 were re worked three times and need some better design going forward in the future
The hydrogen seals were “Bottoming out” on the outer race and thus were not allowing the inner rings to float as they should
Various workmanship issues from the last overhaul
Inboard collector ring is dished and outboard is not. There were new brushes used on theinboard did that cause the “dishing”
Project Photos
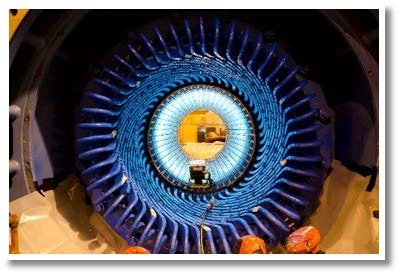
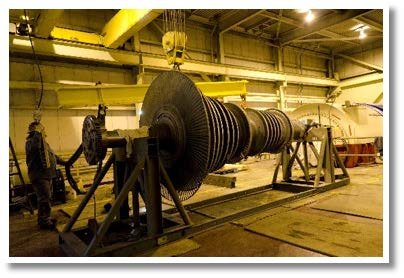
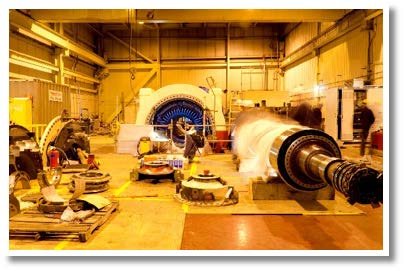
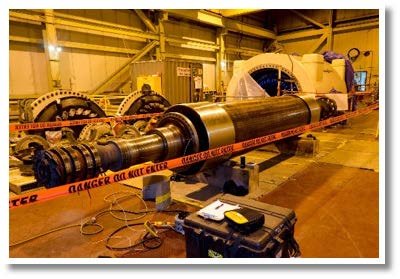
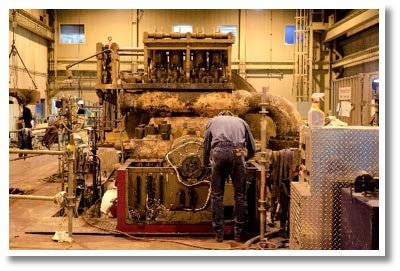

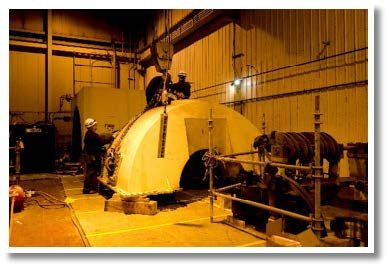
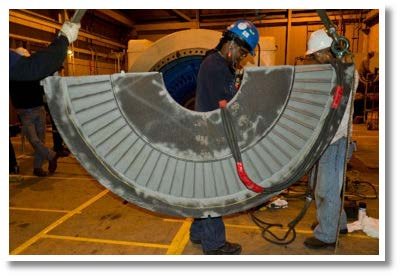
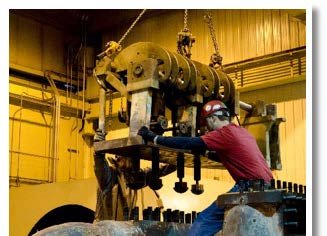
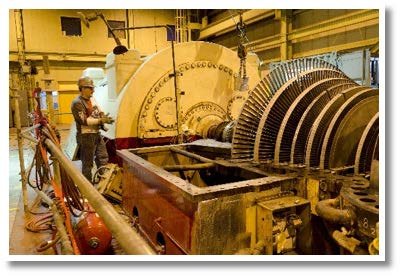
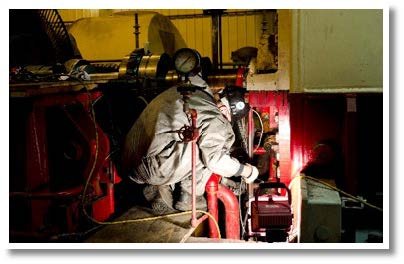
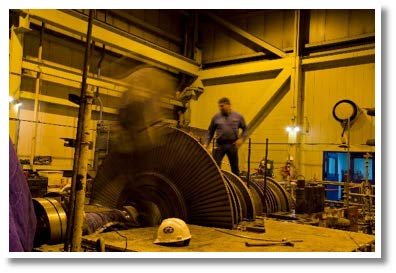
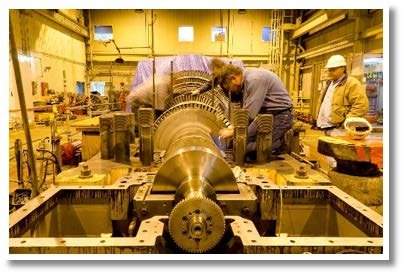
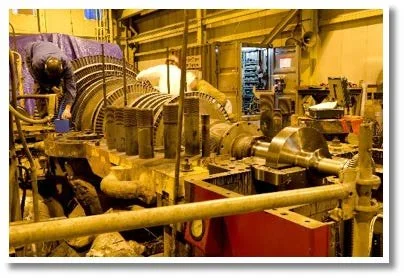
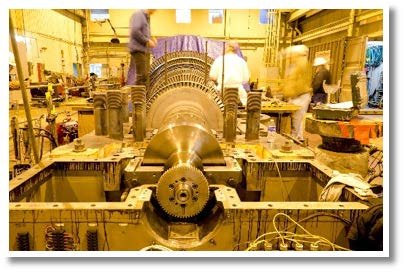
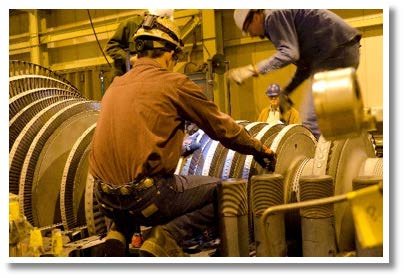
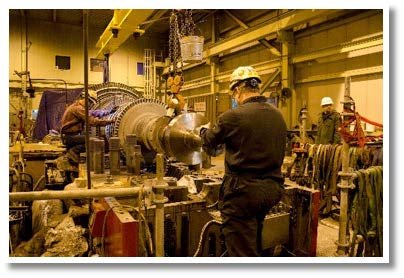
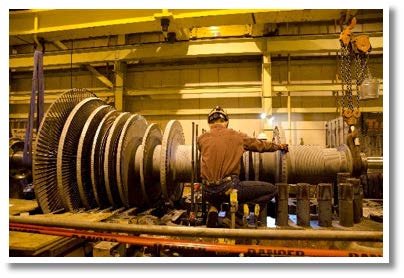

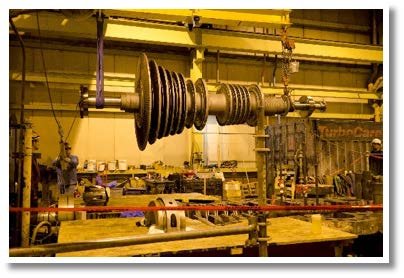
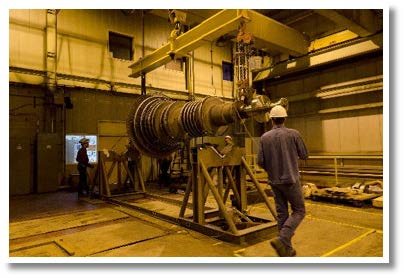